Benefits of CNC 5-Axis Milling
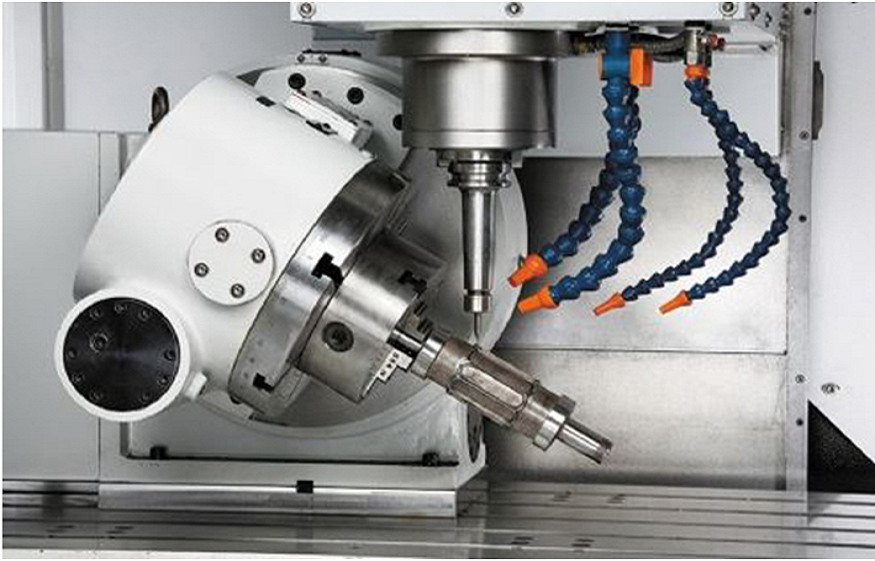
As technology advances, more and more businesses are beginning to adopt CNC machining as a way to create products and components.
CNC machining can be used for a variety of purposes including milling, drilling, turning and grinding; however, 5-axis CNC milling has become increasingly popular due to its accuracy (reduced scrap rates), versatility (fewer setup times) and efficiency (fewer steps creating parts with Complexity). These reasons make cnc 5 axis mills a desirable investment for business owners who are looking save money while not compromising on product quality or precision!
Additionally because every possible angle is achievable with 5 axis mills post processing becomes much simpler as does fixturing saving time & money on potential redesigns later down the line!
Minimized Setup
CNC 5-axis milling is a process that uses five axes to create more complex shapes than traditional 3-axis milling. This process has many benefits that make it an attractive choice for manufacturers. Minimized setup is one of these benefits.
5-axis milling can be used to minimize setup time and increase productivity in the machining of complex parts. 5-axis technology uses a fixed coordinate system, when using 5-axis milling, the part is mounted on a rotary table that allows it to be rotated in any direction. This means that all of the machine’s axes are always in alignment, regardless of the position of the tool or work piece. As a result, there is no need to make frequent adjustments to keep everything in line. This gives the operator the ability to position the part in the most efficient way possible for each operation.
5-axis milling also offers the advantage of being able to machine multiple sides of a part in one setup. This eliminates the need to reposition the work piece or tool between each individual cut, and can significantly reduce the overall machining time for a project. In addition, 5-axis milling can often produce parts with a higher degree of accuracy than traditional 3-axis milling.
Overall, using the 5-axis technology requires fewer setups because the machine’s axes are always in alignment, cutting tools remain in constant contact with the work piece, and more complex shapes can be machined in a single setup. This can lead to increased efficiency and productivity in the manufacturing process.
Complex Designs
The main advantage of 5-axis milling over traditional 3-axis milling is the ability to create more complex shapes and designs. With 3-axis milling, the cutting tool can only move in three directions: up/down, left/right, and forwards/backwards. However, with 5-axis milling, the cutting tool can also move in two additional directions: horizontally and vertically. 5-axis milling machines work by moving the material or work piece in five different directions simultaneously. This allows for a greater range of motion and more versatility when creating designs, that would not be possible with other types of milling machines.
Besides, 5-axis milling machining often use CAD (computer-aided design) software to create the complex designs that they will produce. The operator then inputs the desired cutting speeds and feeds into the machine. The machine will then move the work piece accordingly. With CAD, designers can create models of parts and assemblies that can be viewed from any angle. This allows for accurate determination of how the part needs to be positioned in order to be machined correctly.
Once the CAD model is complete, it can be exported to a CAM program which will generate the tool paths needed to machine the part. The CAM program will take into account the different angles of the 5 axes and create tool paths that are optimized for each individual axis. This ensures that the part is machined correctly and efficiently.
Faster Material Removal
When it comes to cutting metal, speed is often of the essence. 5-axis CNC milling can be used on a variety of materials, including metals, plastics, and composites. The faster the material can be removed, the sooner the project can be completed. 5-axis CNC milling machines typically have higher power and speed capabilities than their 3-axis counterparts. That’s one of the advantages of 5-axis CNC milling machining.
By moving the material in multiple directions at the same time, this type of machining can remove material much faster than traditional 3-axis machining. This means that the material can be removed in a shorter amount of time because the machine does not have to stop and start again in order to change directions.
In addition, 5-axis CNC milling machines can also perform multiple operations at the same time. For example, while one tool is removing material, another tool can be preparing the next area for milling. This helps to increase the overall efficiency of the process and can further reduce the amount of time required to remove material.
Conclusion
Another advantage of 5-axis milling is the ability to create parts with smaller tolerances. This is because the cutting tool can move in very small increments, allowing for greater precision. By combining the power of CAD with the precision of CNC, these machines can produce the complex parts that require a high degree of precision, and that would be impossible to create with 3-axis machining.
As a result, 5-axis CNC milling is an extremely versatile and powerful tool for metalworking. The milling machine removes material from the workpiece until the desired shape is achieved. This type of machining is very versatile and can be used to create small, precise parts for medical devices, aerospace components, and other delicate applications. And best of all, it can help you get the job done faster.
All in all, 5-axis milling machines are some of the most precise and intricate machines available today. Many companies use 5-axis milling machines to create prototypes or one-of-a-kind products.